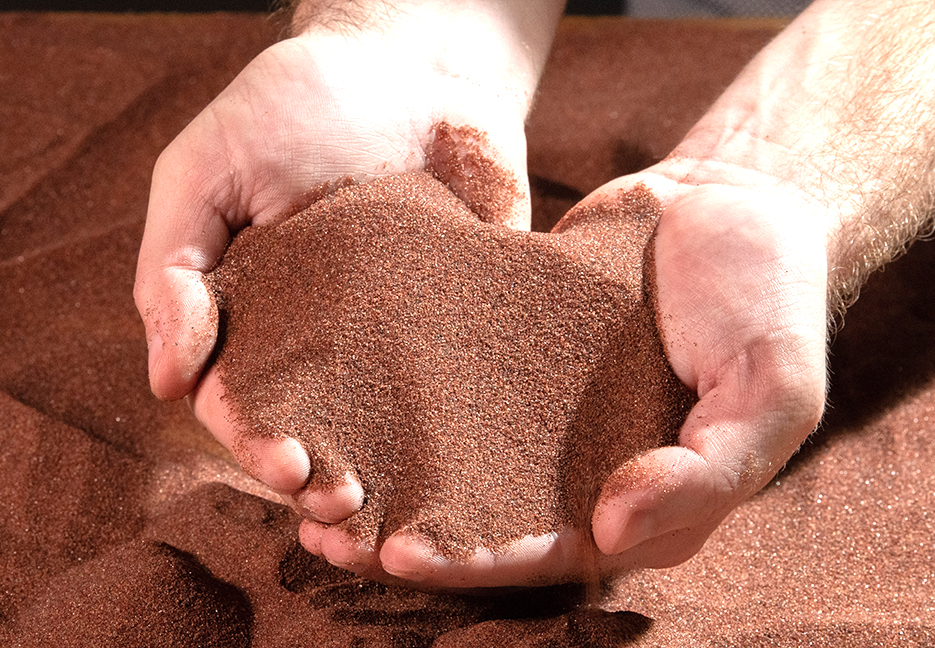
For the second time in recent years, Adirondack garnet mined from Barton Mines’ quarry in Johnsburg and processed into an abrasive blasting product at the company’s plant in Indian Lake is playing a key role in the refurbishment of a U.S. Navy aircraft carrier.
Barton Mines is a family-owned company, headquartered in Glens Falls, that has been mining garnet in the Adirondack region since 1878.
Barton Adirondack 30/60 CG garnet blast abrasive is being used to clean and prepare the entire steel exterior of the USS John C. Stennis for the application of a new protective coating. The work is being performed by Barton’s customer Mid-Atlantic Coatings, Inc. (MAC) at Newport News Shipbuilding in Virginia where the Stennis is in the midst of a four-year refurbishment.
The same Barton product was used by MAC on the USS George Washington during the surface preparation phase of that ship’s refurbishment, which began in 2017.
“Barton products are American-made by a family-owned company and we’re immensely proud and humbled to serve the brave men and women who serve our nation every day,” said Barton CEO Randy Rapple. “Whenever we see or hear about the USS Stennis or George Washington, Barton employees, many of whom are veterans themselves, will know they played a part in keeping the ships at sea.”
Barton’s garnet blast abrasive is propelled against the ship’s steel by high-pressure air in a process commonly known as sandblasting. The sharp, angular garnet crystals quickly clean and smooth the steel surface, preparing it for a new coating.
Company officials said Barton’s Johnsburg quarry is widely recognized as yielding the hardest, sharpest garnet crystals in the world. Barton garnet is also the preferred blast abrasive for many customers for its human and environmental safety, as it is 100 percent natural and free of any heavy metals.
MAC President Vincent D’Auge said the company spent months testing a wide variety of materials that met military specs for blasting. But testing showed that BARTON 30/60 CG garnet was the most productive and met all environmental, health and safety requirements.
“The things Barton did as a supplier on the George Washington project showed me that they care and that I can rely on them,” D’Auge said. “We chose 30/60 CG garnet as the best value based on the performance, consistency, cleanliness and safety of the product, and the outstanding customer support. MAC and Barton are industry leaders, and both our companies stand by our commitments. I knew we could depend on Barton.”
Barton garnet blast abrasives are used for the manufacture of civilian and military aircraft, the construction and maintenance of armored vehicles, the production of titanium medical implants, and many other purposes. Barton also manufactures garnet abrasives for waterjet cutting, which are used in a variety of industries, including aerospace and aviation, automotive, electronics, architecture, creative arts, medical, and defense.
The company said a Barton waterjet abrasive product was used to cut and shape the blades of the U.S. Luge team’s sleds for the 2022 Winter Olympics. Barton products have also been used in the maintenance of the National Oceanic & Atmospheric Administration’s aircraft fleet, and in the manufacture of electric vehicles, Broadway theater sets, bullet-resistant glass, and many other products.
Since 1983, mining and initial mineral processing has occurred at the company’s quarry and mill on Ruby Mountain in the town of Johnsburg, hamlet of North River. Final processing takes place at the company’s plant in Indian Lake.
Barton officials said the company employs approximately 125 people, provides wages and benefits of more than $15 million per year, spends approximately $7 million annually with other local businesses, and pays more than $400,000 annually in local school and property taxes.